The Production
All products in the EUROLUX series are made from a high-quality aluminum alloy sourced from German smelters using the tried-and-tested “MADE IN GERMANY” permanent mold casting process and are produced piece by piece by hand.
- The process has been the same for decades, even though some technical developments have of course taken place.
- A very, very rough overview of the production process:
- The aluminum is melted at approx. 800 degrees and then poured into a mold by hand casting.
- After the casting has cooled down and been removed from the mold, the “sprue” is sawn off.
- Possible small irregularities are removed by turning or grinding.
- The induction coating is then applied (aluminum is non-magnetic and therefore inherently non-inductive).
- Now apply the non-stick coating.
- The finished bodies are now stored until they are ordered. After the order is placed, the selected handles are assembled, the goods are packed – and dispatched.
About the coating
In our classic series, we work with the sealing of our LuxTec® coating. toothed and sealed.
The following diagram shows the structure of a classic EUROLUX ® pan.
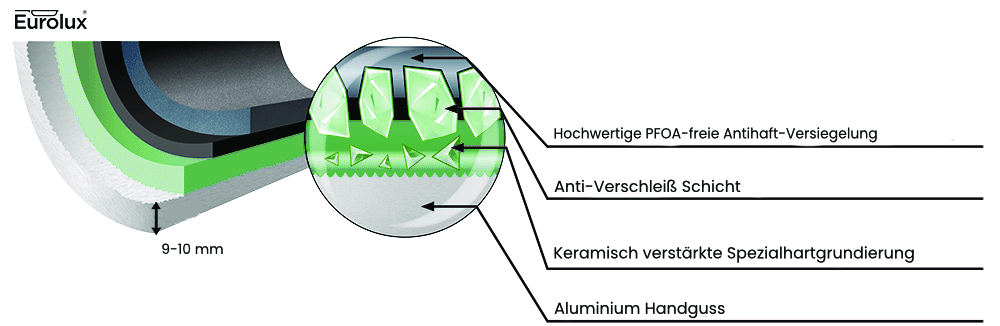
The material: aluminum
A few facts:
- Aluminum is the most abundant metal on earth.
- After iron, it is the second most important metal for industry.
- Aluminum has been used in production since around 1850.
- Aluminum conducts heat seven times faster than iron or steel.
75 percent of the aluminum ever produced is currently still in use.
The really impressive thing, however, is “that around 75 percent of the aluminum ever produced is currently still in use. “ A large proportion of this has probably already been recycled several times and is already being reused by the third or fourth generation. It is therefore quite possible that one of our pans still contains aluminum that was extracted in 1888. In Germany, more recycled aluminum is produced than new aluminum. Up to 96 percent is recycled in the transportation and construction sectors and around 90 percent for packaging. The production process for new aluminum is energy-intensive. Compared to the initial production of the metal, the recycling process requires just five percent of the energy required. Aluminum is doubly sustainable.
Conclusion: Thanks to its conductivity and the fact that aluminium is recycled again and again, our cookware is doubly sustainable. Because the conductivity saves energy when cooking.
Source: allesueberalu.de
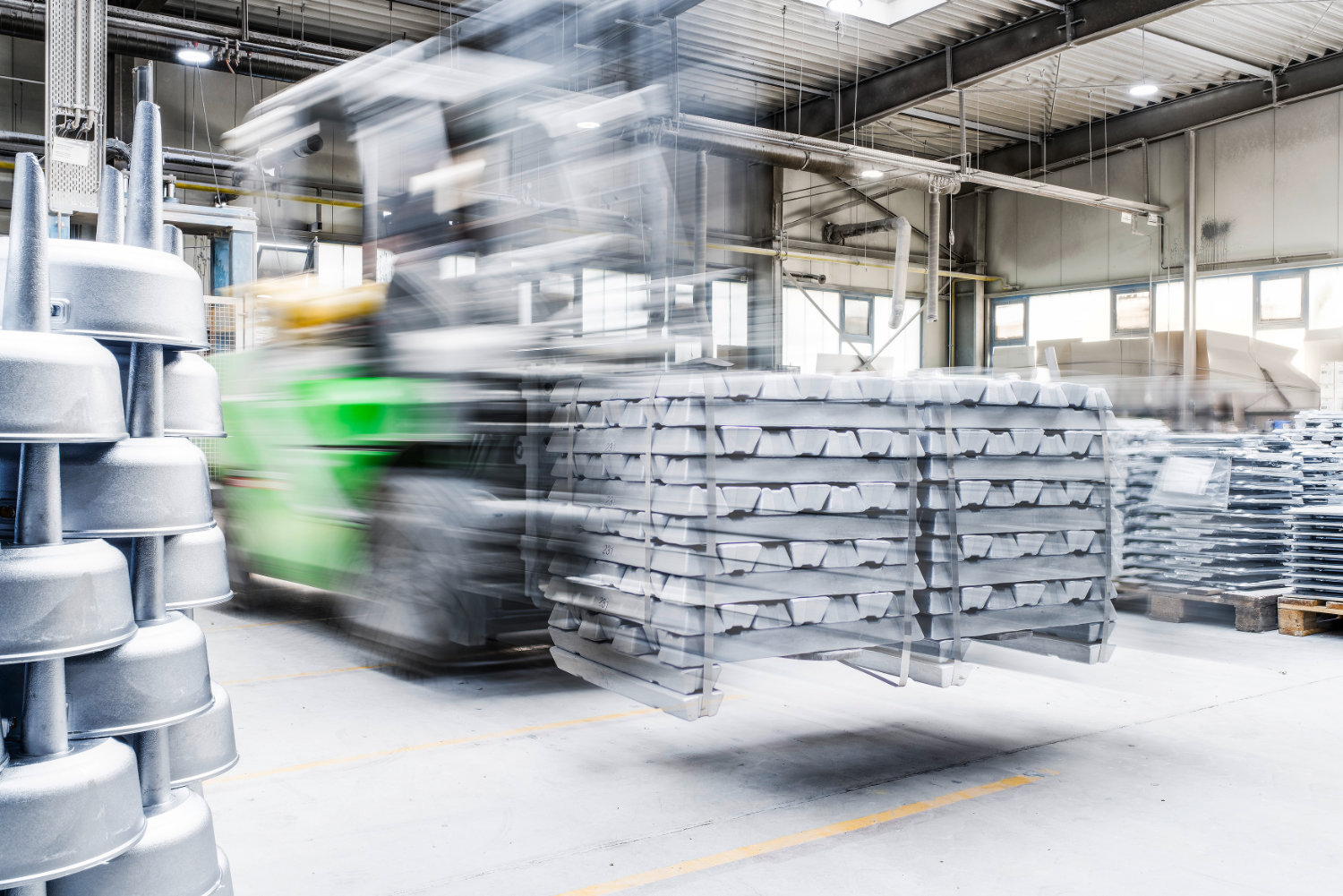
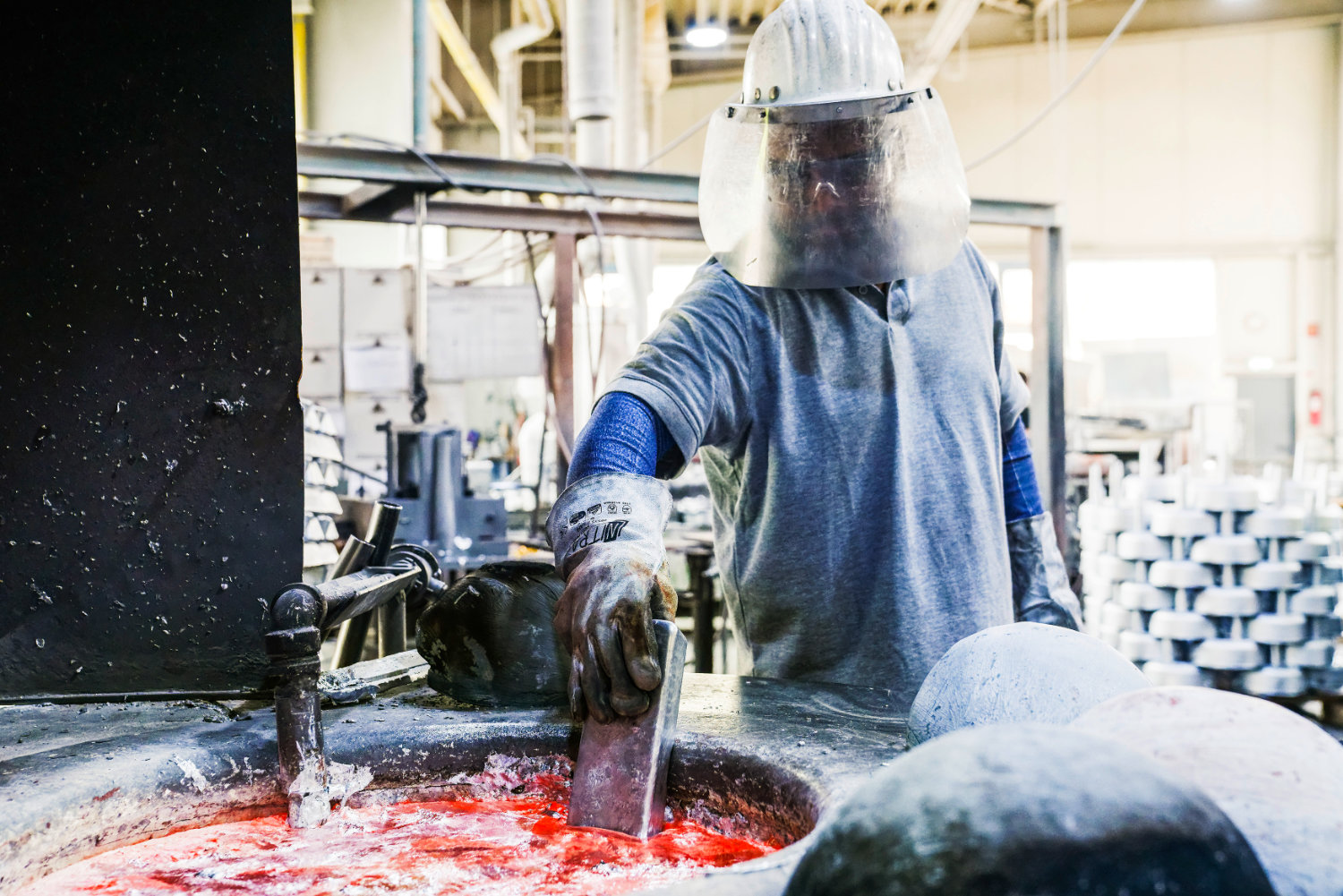
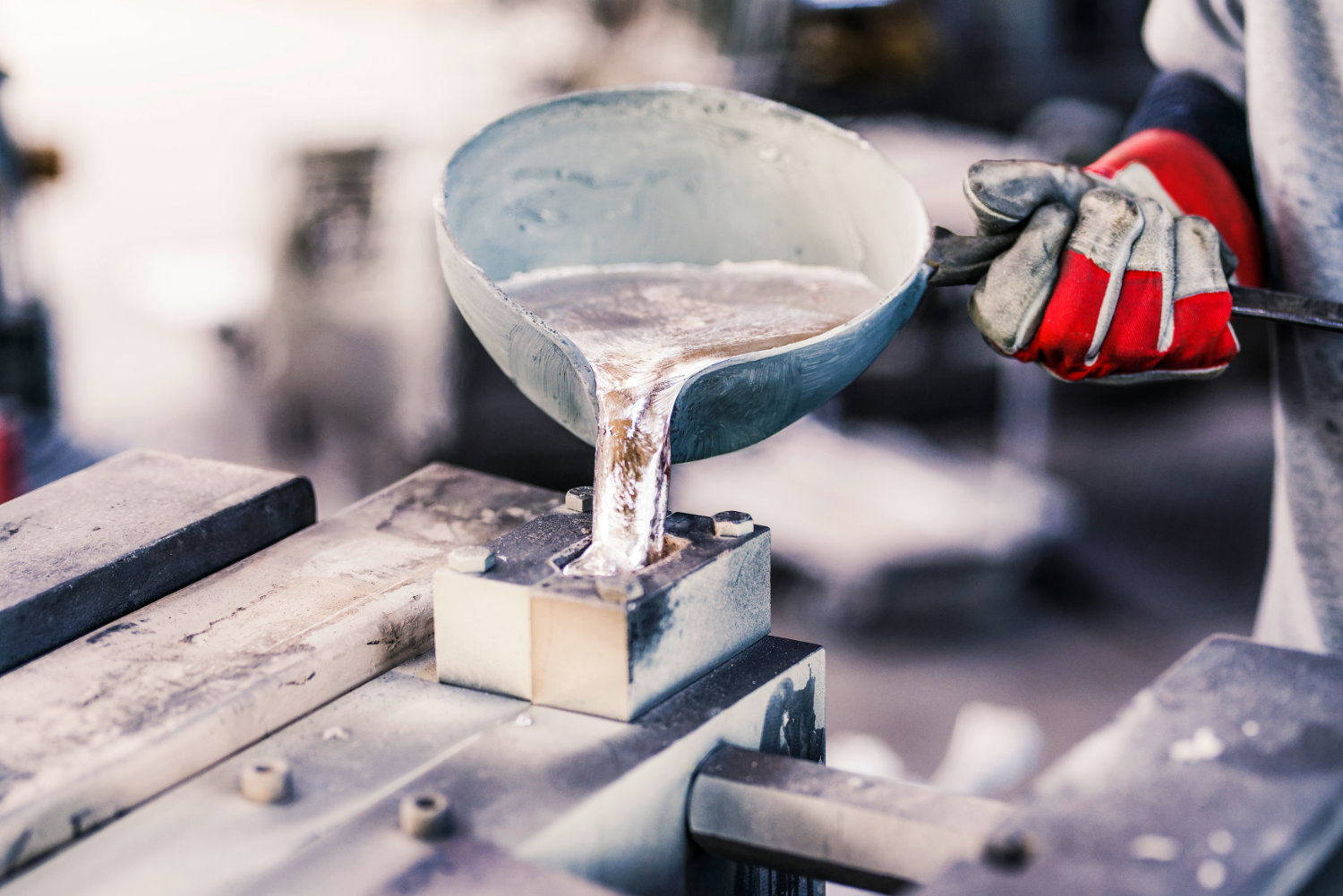